accuracy, reliability, repeatability, and verifiability
Manufacturing has always had a need for accuracy, reliability, repeatability, and verifiability. Today that need is higher than it ever has been. That’s because manufacturing success now demands that each and every component that makes up a functional assembly fit together to produce an end product that performs as designed and is as nearly identical as possible to the others produced. Modern Manufacturing will start to see pressing needs in the long term of their industry.
In production environments, the standard response to this need usually involves building very precise tooling and fixtures that, once put into use, face near-constant adjustment due to unpredictable variations in assembly components. The scrap and rework that results from trying to get it right are simply tallied up as part of the cost of doing business.
These costs can be avoided.
Avoid Scrap and Rework
Integrating sensors, powerful software and data analysis tools with precision presses brings not only the power to perform precision press-fit assembly tasks, but also the ability to gather data and generate signature curves of the process while it happens. With smarter assembly systems, manufacturers can press to a programmable position, press to an offset, or press to a rate of change in order to achieve consistent part success. “Press and hope” followed by “sort and toss” gives way to establishing parameters for perfect parts (at times with looser tolerances or less press force necessary than originally thought) and then cloning them with regularity.
How It’s Done
The best systems involve the integration of high-level electronics, force and distance sensors, and precision press mechanics with intuitive software. This allows a press to have a sense of feel or touch. Signature analysis, unlimited gaging points and integrated programming language with a complete math engine allow for generating signature curves, analyzing data, and compensating on the fly, creating the utmost confidence that a good part is being made every time. Such “intelligent presses” with high-precision closed loop control allow for a complete rethinking of many assembly manufacturing applications.
Millions of steering-column hinge mechanisms, for example, must be assembled and pressed relative to how they function. The possibility of testing their function during assembly not only can compensate for component variations, but also offers significant process and cost savings.
For this application, Promess provided two Servo Presses designed to operate in conjunction with each other. Servo Press 1 presses and forms the assembly’s rivet/pivot pin while servo press 2 actuates the hinge mechanism back and forth. To work properly, both presses must be capable of measuring and controlling force and distance very accurately while being able to communicate with each other and record data.
The amount of force applied to form the rivet/pivot pin in place directly affects how much force is necessary to make the hinge mechanism function. The two servo presses work together forming the rivet/pivot pin and simultaneously exercising the hinge mechanism until the correct “exercise force” is reached.Once the exercise force is reached, servo press 2 tells servo press 1 to stop. Servo Press 2 then completes a final exercise motion to ensure the assembly is within the correct “exercise force” tolerance. The data is then stored and a now-verified quality functional part moves on to the next station. In this case, such a “press to function” method makes good parts every time despite variations in the components that make up the steering column hinge mechanism assembly.
Limitless Possibilities
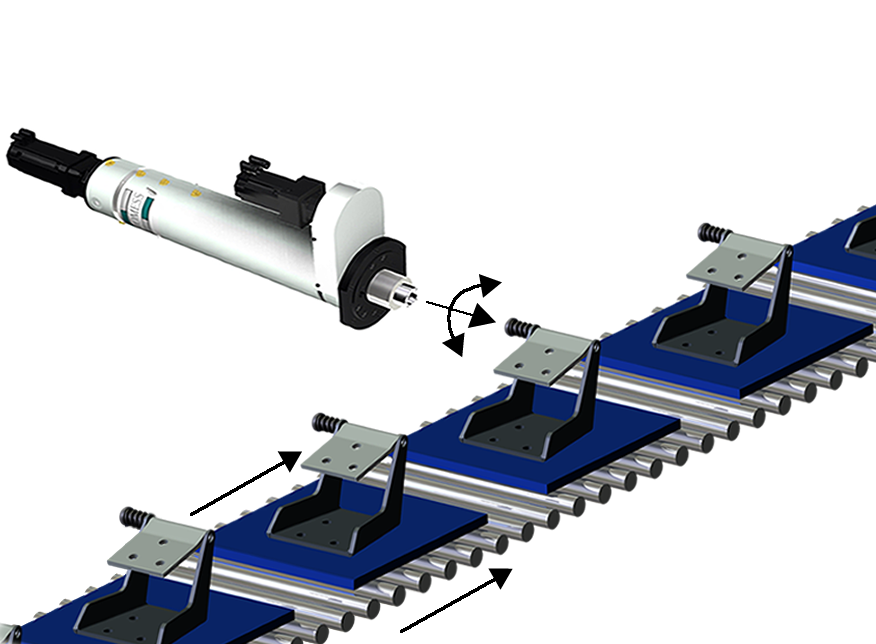
A REMAP system shown coupling to and torque-to-turn testing automotive door hinges.
Think of anything where critical motion involves rotation (power tools, jet engines, rack-and-pinion steering gears, or axle differentials) and you’ll find roller bearings. Having an servo press where the ram rotates (REMAP) in addition to extending and retracting means such a press system can be programmed to press and monitor rotation, press force and torque.
These REMAP systems can also monitor a bearing’s inner race with a digital probe to determine how much lash is on the bearing. Breakaway torque and running torque can be tested under a range of load conditions during assembly, meaning bearings could be simultaneously tested, pressed into place, and preloaded. The improved consistency that results, verified by torque versus force curves, equals longer life, improved fuel economy, more horsepower, and improvement in a variety of other possible functions that the final assembly delivers.
Preloading and monitoring force, position, and torque limits assures critical bearing quality.
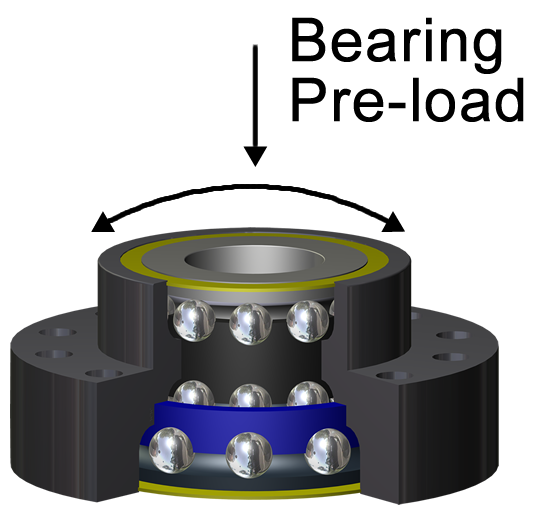
Promess’ state-of-the-art presses can also monitor press velocity, which is critical in an application pressing batteries for medical devices. These batteries have upper and lower components and require press force from both directions to compress the conducting powder inside into a solid.
As you get closer to the target force, in the range of 50,000 lb (22,500 kg), EMAPs are smart enough to slow down and target the force exactly. In battery manufacturing, pressing with too much force has as many drawbacks as pressing with too little. In addition, in order to eliminate problems from occurring when you release the pressure, it is critical that both sides are pressed with the same amount of force and to the same distance. The EMAPs can be synchronized, and communicate with each other to stay synchronized, and they can generate the force and position curves to prove it.
Gearboxes and Backlash
In-process monitoring and real-time response to variations in press-fit assembly can do more than simply spot mistakes. It can guarantee that a bad product never leaves the station.
Take the issue of backlash in gear assemblies. Backlash testing is most often approached in one of two ways: static or dynamic. Static testing involves the output, or final driving gear, being held in a fixed position while torque is applied in both directions to the input gear. The calculated difference is the static backlash of that particular gear assembly at that particular mesh point. Dynamic testing involves the gear being rotated to incorporate all mesh points as torque is applied. With Rotational Electro-Mechanical Assembly Presses, each with high-precision rotary encoders, all forces can be captured, stored, plotted, and displayed in both directions. This data can then be used to determine minimum, average, and maximum values for go or no-go decisions before the assembly ever leaves the station. Since the REMAP’s ram rotates and can capture rotational position information in addition to torque, press force, and angle, it becomes an exceptional tool for torque-and-turn tests. It can establish breakaway torque (the restraining torque that has to be overcome to start rotation of one ring of the bearing while the other remains stationary), average running torque (the mean torque encountered during rotation), and peak running torque, all under varying axial load conditions. All data can be collected and plotted in torque and force curves.
Adding sensing and data-gathering capabilities to press-fit applications does not have to be a science-project nightmare of myriad custom components. Quite the contrary, establishing intelligent press-fit systems that can monitor and establish upper and lower control limits for pressing, testing, and assembling an infinite number of applications is limited only by the engineer’s imagination.
Manufacturers spend enormous sums of money to produce ultraprecise parts that are assembled with technologies that have not changed significantly in a century. Why not spend less on the components and assemble them with a smart system that can accommodate dimensional variations and still produce functional products? All that’s needed to make that happen is a willingness to step back and look at the possibilities inherent in today’s intelligent assembly technologies. Function is the consumer’s measure of quality, and function ought to be the manufacturer’s as well.