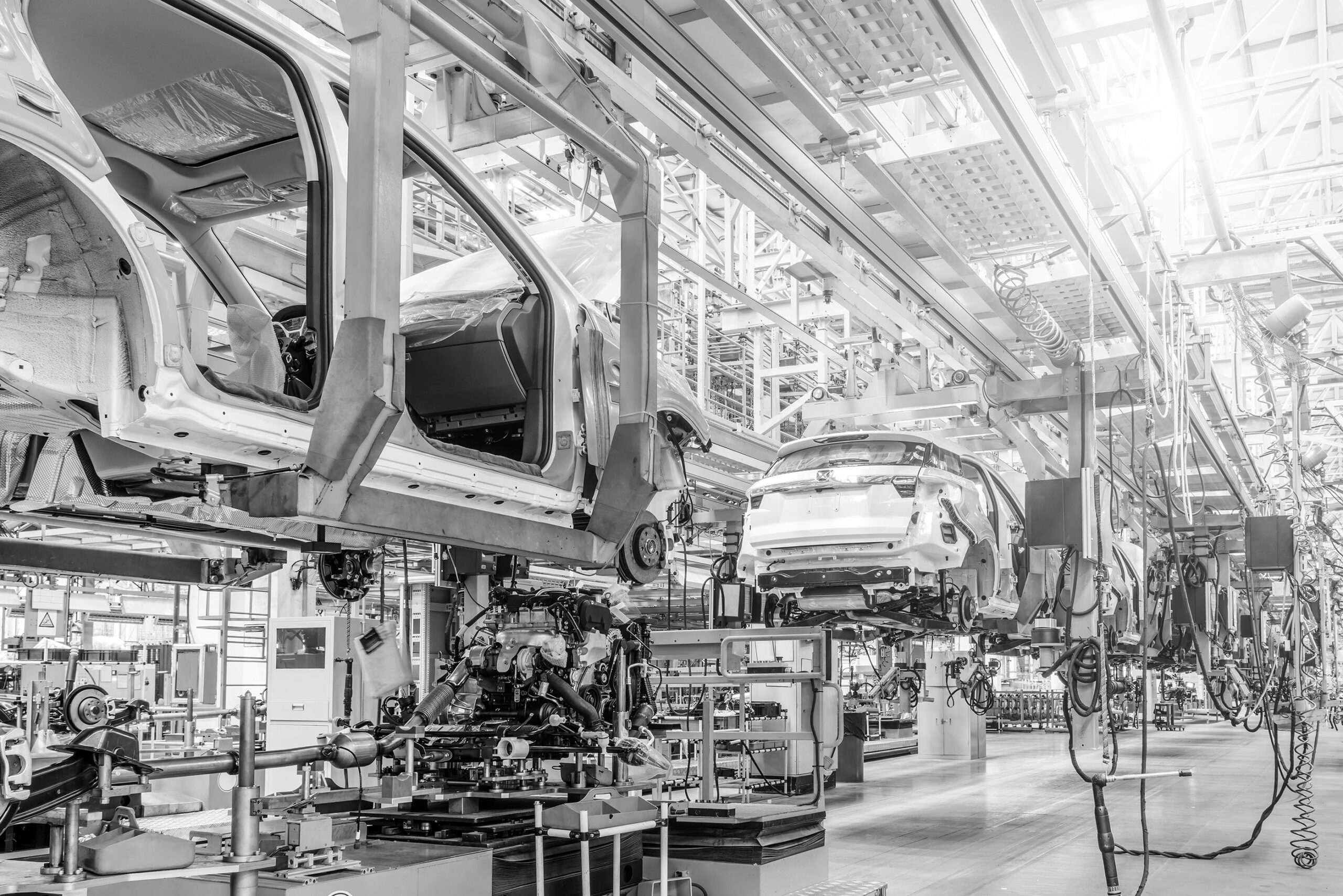
CASE STUDIES
Engineering Solutions for Manufacturing Challenges
At Promess, we specialize in delivering precision engineering solutions to overcome manufacturing challenges. As a leader in intelligent assembly and test systems, we provide manufacturers across industries with advanced technology that ensures accuracy, repeatability and reliability.
Case Studies
Circuit Board Assembly
Reducing defects and energy consumption in circuit board assembly by utilizing Promess Compliant Pin Press Assembly A leading …
Assembling Automotive Belt Tensioners
Manufacturing automotive belt tensioners requires a highly coordinated assembly system that can precisely control both linear and rotational …
Desk Chair Bushing Testing
In the manufacturing of ergonomic desk chairs, one of the most critical components is the Torsion Bushing. This …
Cross Thread Prevention
A manufacturer faced significant quality issues when assembling two sub-assemblies that needed to be threaded together and torqued …
Seat Recliner Mechanism Testing
In the automotive industry, ensuring the safety and reliability of every component is crucial. One of the most …
Precise Torque Test in Brass Fitting Insertion
In the world of manufacturing, even the smallest component can cause significant headaches when quality issues arise. This …
Assembly Universal Joints | Staking Application
In the world of automotive manufacturing, precision and reliability are critical. Universal joints, which connect the driveshaft to …
Trigger Pull Test Handgun Manufacturing
A manufacturer of handguns for the US Military sought a solution to verify that each firearm component met …
Composite Compression
The most common assembly process for composite parts is compression molding. Material is inserted between coordinated metal dies …
Hydraulic Pressure Relief Valve is Assembled and Tested Via EMAP
Valve manufacturers today are able to inspect parts during assembly rather than after to produce near-perfect fluid pressure …
Case Study: Battery Assembly
Customer was looking for a turnkey assembly cells that had flexibility, data storage and management, but more importantly, …
Case Study: Water Pump Assembly
In the assembly and manufacturing of automotive water pumps, there are various components that need to be pressed …
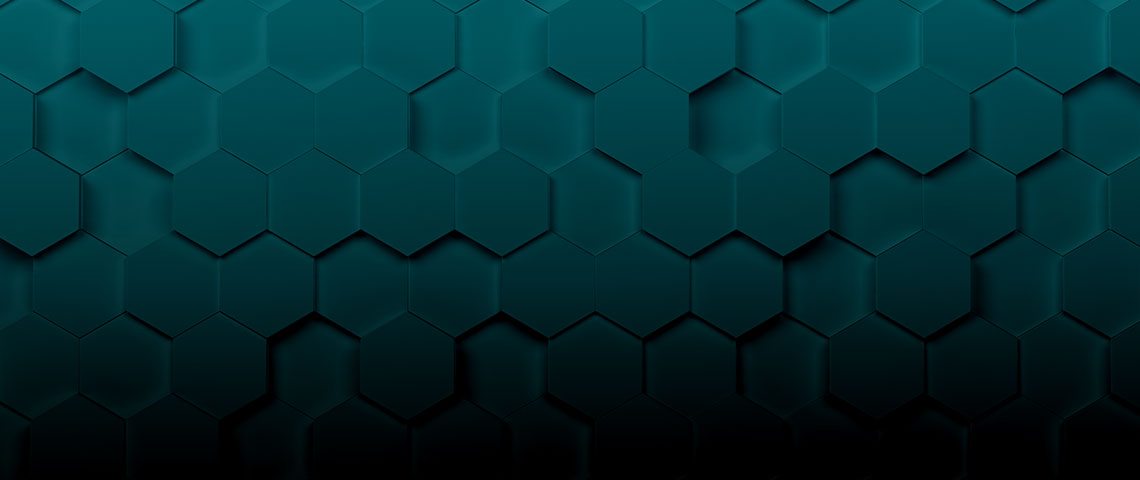
Do You Have an Application?
Talk to one of our expert engineers or learn more about proving your
application in our Process Development Center.