Case Study #1550 | EMAP
POWER STEERING PUMP ASSEMBLY
Challenge
On a power steering pump assembly, the pulley must be assembled onto the pump shaft relative to a machined surface on the pump housing.
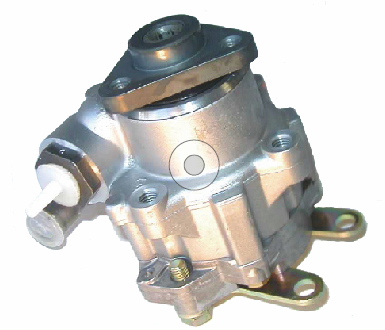
Requirements
- The pulley needs to be assembled onto the pump shaft relative to three mounting flanges located on the pump housing. The final position must be based on an average of three external position transducers
- The pulley cannot be pressed onto the shaft. The shaft must be pulled into the pulley hub while the pulley is supported. This is to prevent any internal components (bearings or seals) from being damaged, which could cause premature pump failures
- The machine must be able to assemble different models of pumps with quick change over.
Solution
- The Promess Electro-Mechanical Assembly Press (EMAP) Model: EMAP-20 (4,500 lbs. capacity)
- A second servo motor (provided by Promess) to control the threading of the tooling into the pump shaft
- Three external position transducers. (Provided by Promess)
The Promess EMAP is the best solution because it is a closed-loop press system with multi-axis control capability. The Promess motion controller controls both the press and the second servomotor. The analog outputs from the three external position transducers used to measure the critical dimension are also fed directly back into the Promess motion controller.
The application requires that the pulley be assembled onto the shaft relative to three machined mounting flanges located on the pump housing. The final position must be based on an average measurement from the three position transducers. Using a master part and the Master feature within the Promess software, the position transducers are mastered to establish the zero position. The press will then pull the parts together to this position every time.
During the assembly operation, the parts are pulled together just short of the desired final position. The Measure command then reads the deviation from the master, calculates an offset based on the average of the probes and adjusts the depth of press that amount. The Promess system will then recheck the offset from the master and verify that it is within the part tolerances. If not, the press can be set up to correct again. The EMAP also gauges the part and monitors the force versus position signature to ensure that the parts have the proper interference fit.
Process sequence:
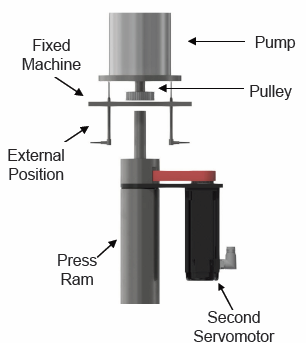
- The ram extends up so tooling goes through pulley. The thread tooling is spring loaded
- The second servomotor turns the thread tooling a set number of rotations to thread tooling into shaft
- The ram retracts to a programmed position. The shaft is pulled into the pulley just short of final desired location
- The Measure command measures the deviation from the master, calculates the offset based on the average of the three position transducers and then adjusts the ram using the offset
- The Measure command checks if the pulley is within the acceptable tolerances. The press can correct again if necessary
- The ram extends up to release load off the tooling
- The second servomotor unthreads the tooling
- The ram retracts to a programmed position for unloading and loading of parts
Results
The pulley must be assembled onto the shaft to a tolerance of ± 0.25mm and ± 0.15mm, depending on the pump. The average of the three external position transducer readings along with the measure function achieves a tolerance range of ± 0.05mm or better. Total setup time to set up the two programs was only 30 minutes. The system is capable of tolerances 3 to 4 times better than the old process.
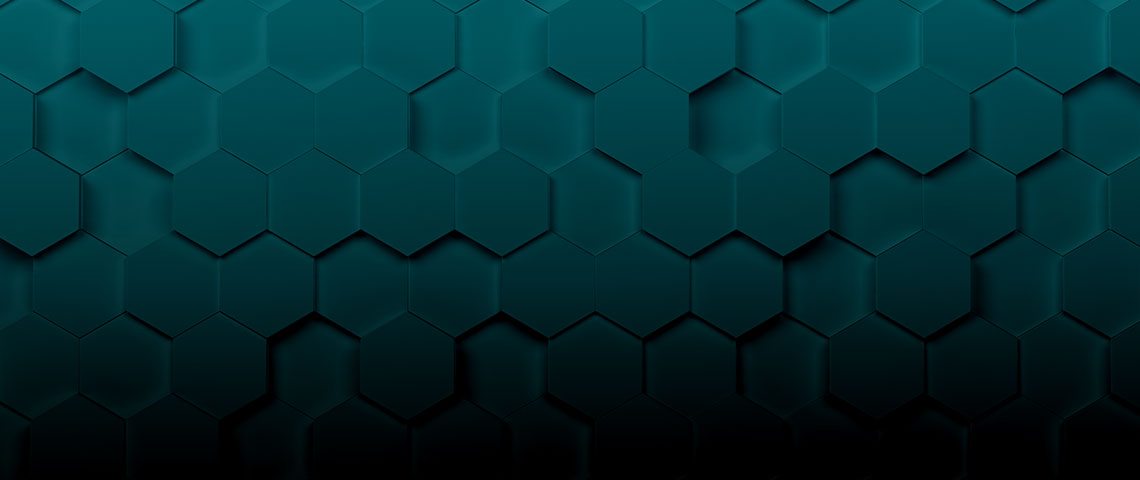
Do You Have an Application?
Talk to one of our expert engineers or learn more about proving your
application in our Process Development Center.