Case Study #1910 | EMAP
REPLACING A HYDRAULIC PRESS
Challenge
Hydraulic presses cost less than servo presses right? Wrong. While the up-front price of a servo press is almost always higher than that of a hydraulic press, the benefits of a servo press more than make up for the difference.
Recently, a large pump manufacturer came to Promess with a problem. They were using a hydraulic press to insert a bearing into a housing. The hydraulic press was going to full pressure every cycle, as hydraulic press was going to full pressure every cycle, as hydraulic presses do. This resulted in too much force being applied to some parts, leading to premature failures of the pump.
The problem was that there was no way to detect when it happened, or how much force was too much for any individual part. To compound the problem, the failures cut the life of the pump by about ninety-five percent, meaning the pumps passed all internal tests, but failed early on once they were in the field, leading to a 10% -20% return rate.
Solution
Using the Promess Electro-Mechanical Assembly Press (EMAP) with a Promess motion controller, the bearing insertion can be started and taken to a certain point, then pressed to a relative force from there.
This means that every bearing can be pressed with only enough force to ensure that particular bearing is fully seated, and no more. During this cycle, process data, including a force vs. distance curve, can be recorded. All data can be stored in a database, along with other relevant cycle information like data and time, serial number, and tolerances, allowing a full record of every part to be maintained for traceability.
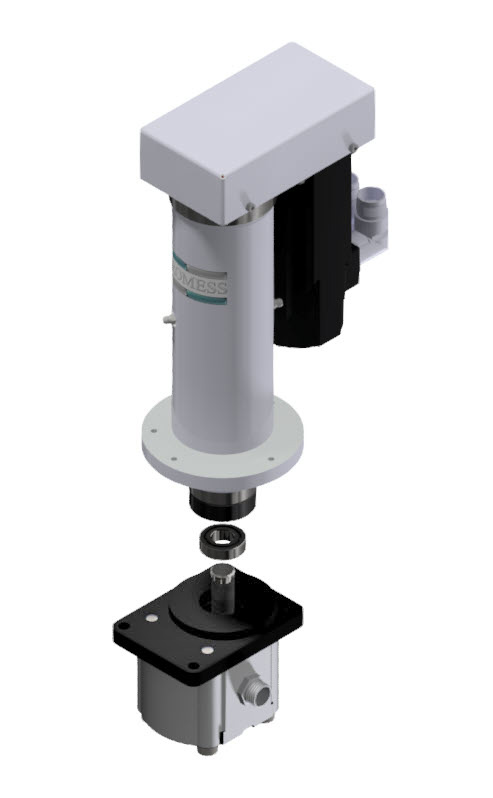
After implementing the “more-expensive” Promess EMAP, the pump failure issue completely disappeared, saving the company $1,000,000 in warranty costs in the first year alone.
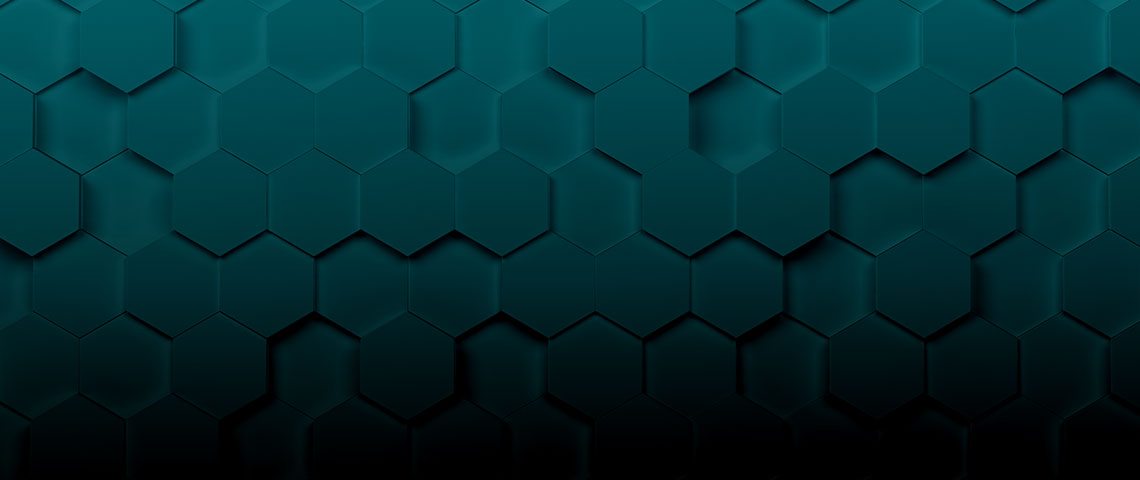
Do You Have an Application?
Talk to one of our expert engineers or learn more about proving your
application in our Process Development Center.